Назначение лакокрасочных материалов
Покрытие внешней поверхности стальных труб имеет решающее значение для предотвращения ржавчины. Ржавчина на поверхности стальных труб может существенно повлиять на их функциональность, качество и внешний вид. Таким образом, процесс нанесения покрытия оказывает значительное влияние на общее качество продукции из стальных труб.
-
Требования к лакокрасочным материалам
Согласно стандартам, установленным Американским институтом нефти, стальные трубы должны противостоять коррозии в течение как минимум трех месяцев. Однако возрос спрос на более длительные периоды защиты от ржавчины, и многим пользователям требуется устойчивость в течение 3–6 месяцев при хранении на открытом воздухе. Помимо требования долговечности, пользователи ожидают, что покрытия будут сохранять гладкую поверхность, равномерное распределение антикоррозионных агентов без каких-либо пропусков или капель, которые могут повлиять на визуальное качество.
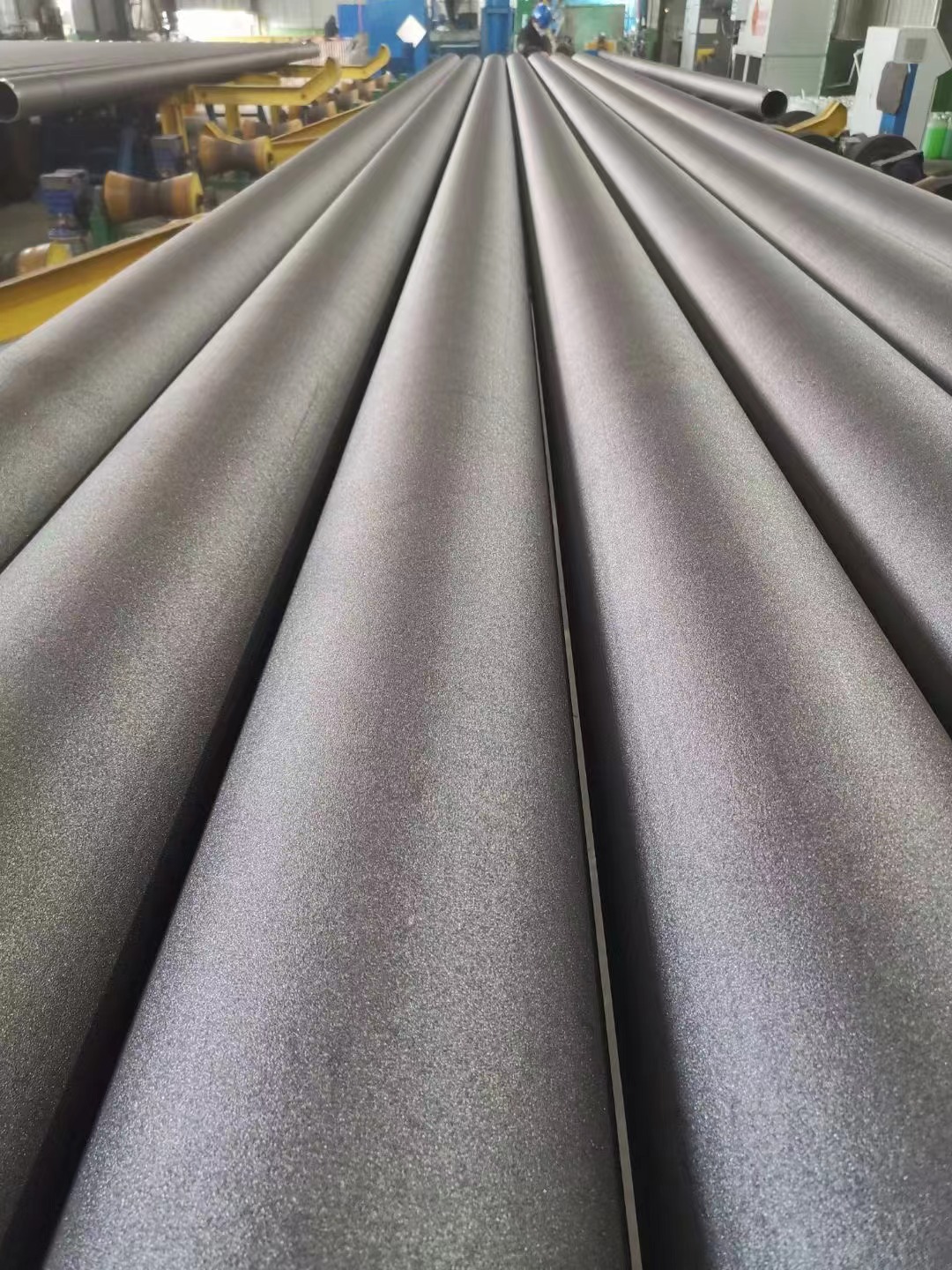
-
Типы лакокрасочных материалов и их плюсы и минусы
В городских подземных сетях трубопроводов,стальные трубывсе чаще используются для транспортировки газа, нефти, воды и многого другого. Покрытия для этих труб эволюционировали от традиционных асфальтовых материалов до полиэтиленовых смол и эпоксидных смол. Использование покрытий из полиэтиленовых смол началось в 1980-х годах, и с изменением сфер применения компоненты и процессы нанесения покрытий постепенно совершенствовались.
3.1 Нефтебитумное покрытие
Покрытие из нефтяного асфальта, традиционный антикоррозионный слой, состоит из слоев нефтяного асфальта, армированных стеклотканью и внешней защитной поливинилхлоридной пленкой. Он обеспечивает отличную гидроизоляцию, хорошую адгезию к различным поверхностям и экономическую эффективность. Однако у него есть недостатки, в том числе восприимчивость к перепадам температур, хрупкость при низких температурах, склонность к старению и растрескиванию, особенно в условиях каменистой почвы, что требует дополнительных мер защиты и увеличения затрат.
3.2 Покрытие на основе эпоксидной смолы
Эпоксидная смола на основе каменноугольной смолы, изготовленная из эпоксидной смолы и асфальта каменноугольной смолы, демонстрирует отличную водостойкость и химическую стойкость, коррозионную стойкость, хорошую адгезию, механическую прочность и изоляционные свойства. Однако она требует более длительного времени отверждения после нанесения, что делает ее восприимчивой к неблагоприятным воздействиям погодных условий в этот период. Кроме того, различные компоненты, используемые в этой системе покрытия, требуют специального хранения, что повышает затраты.
3.3 Эпоксидное порошковое покрытие
Эпоксидное порошковое покрытие, представленное в 1960-х годах, представляет собой электростатическое распыление порошка на предварительно обработанные и предварительно нагретые поверхности труб, образуя плотный антикоррозионный слой. Его преимущества включают широкий диапазон температур (-60°C до 100°C), сильную адгезию, хорошую устойчивость к катодному отслоению, ударам, гибкости и повреждению сварных швов. Однако его более тонкая пленка делает его восприимчивым к повреждениям и требует сложных производственных технологий и оборудования, что создает проблемы при применении в полевых условиях. Хотя он превосходит по многим параметрам, он уступает полиэтилену с точки зрения термостойкости и общей защиты от коррозии.
3.4 Полиэтиленовое антикоррозионное покрытие
Полиэтилен обеспечивает отличную ударопрочность и высокую твердость наряду с широким диапазоном температур. Он широко используется в холодных регионах, таких как Россия и Западная Европа, для трубопроводов из-за своей превосходной гибкости и ударопрочности, особенно при низких температурах. Однако остаются проблемы с его применением на трубах большого диаметра, где может возникнуть растрескивание под напряжением, а попадание воды может привести к коррозии под покрытием, что требует дальнейших исследований и усовершенствований в материалах и методах нанесения.
3.5 Тяжелое антикоррозионное покрытие
Тяжелые антикоррозионные покрытия обеспечивают значительно более высокую коррозионную стойкость по сравнению со стандартными покрытиями. Они демонстрируют долгосрочную эффективность даже в суровых условиях, срок службы превышает 10–15 лет в химических, морских и растворяющих средах и более 5 лет в кислотных, щелочных или соленых условиях. Эти покрытия обычно имеют толщину сухой пленки от 200 мкм до 2000 мкм, что обеспечивает превосходную защиту и долговечность. Они широко используются в морских сооружениях, химическом оборудовании, резервуарах для хранения и трубопроводах.
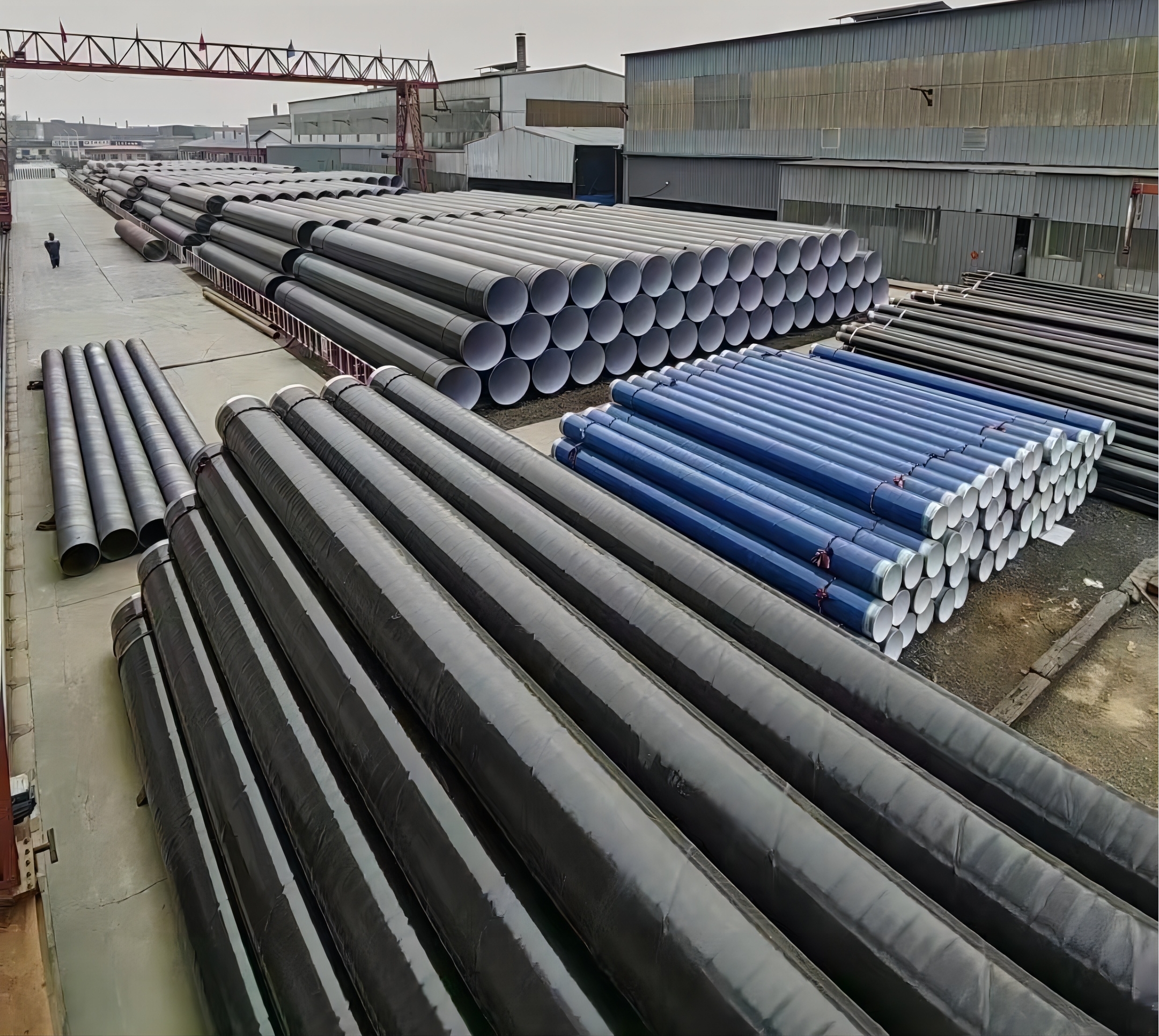
-
Распространенные проблемы с материалами покрытия
Распространенными проблемами с покрытиями являются неравномерное нанесение, подтекание антикоррозионных средств и образование пузырьков.
(1) Неравномерное покрытие: неравномерное распределение антикоррозионных средств на поверхности трубы приводит к появлению участков с чрезмерной толщиной покрытия, что приводит к отходам, в то время как тонкие или непокрытые участки снижают антикоррозионные свойства трубы.
(2) Капание антикоррозионных средств: это явление, при котором антикоррозионные средства застывают, образуя капли на поверхности трубы, что влияет на эстетический вид, но не оказывает прямого влияния на коррозионную стойкость.
(3) Образование пузырьков: воздух, попавший в антикоррозионное средство во время нанесения, создает пузырьки на поверхности трубы, что влияет как на внешний вид, так и на эффективность покрытия.
-
Анализ проблем качества покрытия
Каждая проблема возникает из-за множества причин, вызвана множеством факторов; и связка стальных труб, выделенная качеством проблемы, также может быть комбинацией нескольких. Причины неравномерного покрытия можно грубо разделить на два вида, один из них - неравномерное явление, вызванное распылением после того, как стальная труба попадает в камеру для нанесения покрытия; второй - неравномерное явление, вызванное отсутствием распыления.
Причину первого явления, очевидно, легко увидеть, когда оборудование для нанесения покрытия, когда стальная труба попадает в коробку для нанесения покрытия в 360 ° вокруг в общей сложности 6 пистолетов (линия корпуса имеет 12 пистолетов) для распыления. Если каждый пистолет распыляет из размера потока, то это приведет к неравномерному распределению антикоррозионного средства на различных поверхностях стальной трубы.
Вторая причина заключается в том, что существуют и другие причины явления неравномерного покрытия, помимо фактора распыления. Существует множество факторов, таких как ржавчина на входе стальной трубы, шероховатость, из-за чего покрытие трудно равномерно распределить; поверхность стальной трубы имеет измерение давления воды, оставшееся после эмульсии, на этот раз для покрытия из-за контакта с эмульсией, из-за чего консерванту трудно прикрепиться к поверхности стальной трубы, из-за чего нет покрытия частей стальной трубы эмульсией, в результате чего покрытие всей стальной трубы не является равномерным.
(1) Причина появления висящих капель антикоррозионного агента. Поперечное сечение стальной трубы круглое, каждый раз, когда антикоррозионный агент распыляется на поверхность стальной трубы, антикоррозионный агент в верхней части и по краю будет течь в нижнюю часть из-за фактора гравитации, что сформирует явление висящей капли. Хорошо то, что на линии по производству покрытий завода по производству стальных труб есть печное оборудование, которое может нагревать и затвердевать антикоррозионный агент, распыляемый на поверхность стальной трубы, со временем и уменьшать текучесть антикоррозионного агента. Однако, если вязкость антикоррозионного агента не высока; нет своевременного нагрева после распыления; или температура нагрева не высока; сопло находится в плохом рабочем состоянии и т. д., это приведет к появлению висящих капель антикоррозионного агента.
(2) Причины антикоррозионного вспенивания. Из-за влажности воздуха на рабочем месте дисперсия краски чрезмерна, падение температуры процесса дисперсии вызовет явление пузырения консерванта. Влажность воздуха, более низкие температурные условия, распыление консервантов из диспергированного состояния на мелкие капли приведет к падению температуры. Вода в воздухе с более высокой влажностью после падения температуры будет конденсироваться, образуя мелкие капли воды, смешанные с консервантом, и в конечном итоге попадет внутрь покрытия, что приведет к явлению пузырения покрытия.
Время публикации: 15 декабря 2023 г.